
The Best Air Compressors for Textile Industry
Part 2: Which Kind of Air Compressor to be chosen for Other Purpose in Textile Industry Except Air Jet Looms
In last article, we discussed about the screw air compressors which is used for air jet looms, we Elang has rich experience in the air jet looms and other machines in textile industry, follow our facebook and youtube you will find more pictures and videos:
Facebook: https://www.facebook.com/elangcompressor
Youtube: https://www.youtube.com/c/Elangcompressor
Hereby we continue to discuss the other compressors to be used in textile industry:
Requirements of other part except air jet looms on compressed air quality:
With the improvement of the automation degree of textile equipment and the continuous improvement of modern textile technology, compressed air, as a power source, has been widely used. In addition to air jet looms, it is mainly used in the spinning department and preparation workshop for pneumatic pressurization, pneumatic doffing, air jet twisting, air jet splicing, air jet cleaning and other parts.
Except for the relatively low requirements for the quality of compressed air for pneumatic pressurization and pneumatic doffing (not higher than Level 4 of ISO 8573-1 standard), all the above parts are in contact with the yarn, and the quality requirements shall be the same as those for air jet looms. For places with pneumatic pressurization, the compressed air pressure is generally required to be 0.6~0.8MPa higher than that of air jet looms.
In the selection of air compressors for textile mills, high efficiency, low energy consumption, simple operation and maintenance, reasonable price and other factors shall be taken as the main selection objects according to the requirements of air compressor air delivery and working pressure. In order to ensure the quality of textile products, we must also consider the purification requirements of compressed air (that is, water free, oil free and dust free). In addition, it is required that the air compressor should have good regulation characteristics and energy-saving effect when adjusting the air delivery. The best selection scheme can be determined only by comprehensive analysis and overall consideration of the above issues.
When the textile products required high quality compressed air, the oil free centrifugal compressor or oil free dry oil free air compressor are recommended. In other situation, the oil lubricated screw air compressor is recommended. In general, the screw air compressor and centrifugal air compressors are mostly used in textile industry. As the professional compressor manufacturer, Elang produce also the oil free dry screw air compressor, oil lubricated compressor, centrifugal air compressor, etc, if you have any interested in them, welcome to contact us. Comparison for those different compressors as below:
The main advantages of the screw air compressors:
uniform intake and discharge air, no pressure pulsation, stable operation of the screw air compressor, small foundation, and even no foundation operation. The oil injection screw can obtain a higher single-stage pressure ratio and a lower discharge temperature. It has the characteristics of forced air transmission, that is, the discharge volume is almost not affected by the discharge pressure, and the pressure ratio is basically independent of speed and density. It is especially suitable for parallel operation of multiple compressor units.
Disadvantages: poor air quality, high oil content, need to configure after treatment equipment such as air dryer and air filters, air delivery would be much more smaller than centrifigal compressor.
The main advantages of centrifugal air compressors:
Compact structure, light weight, large air delivery of single centrifugal compressor; It operates under pure oil free conditions, and the compressed air is not polluted by lubricating oil, with higher quality air. High efficiency and energy conservation. The air quality shall meet the Class 1 standard (the international general standard ISO8573-1)
Disadvantages: surge and vibration are easy to occur during startup and shutdown. Multiple units should not be used for parallel operation. When the air delivery and pressure of a single centrifugal compressor can meet the requirements, fewer units should be choose for air supply.
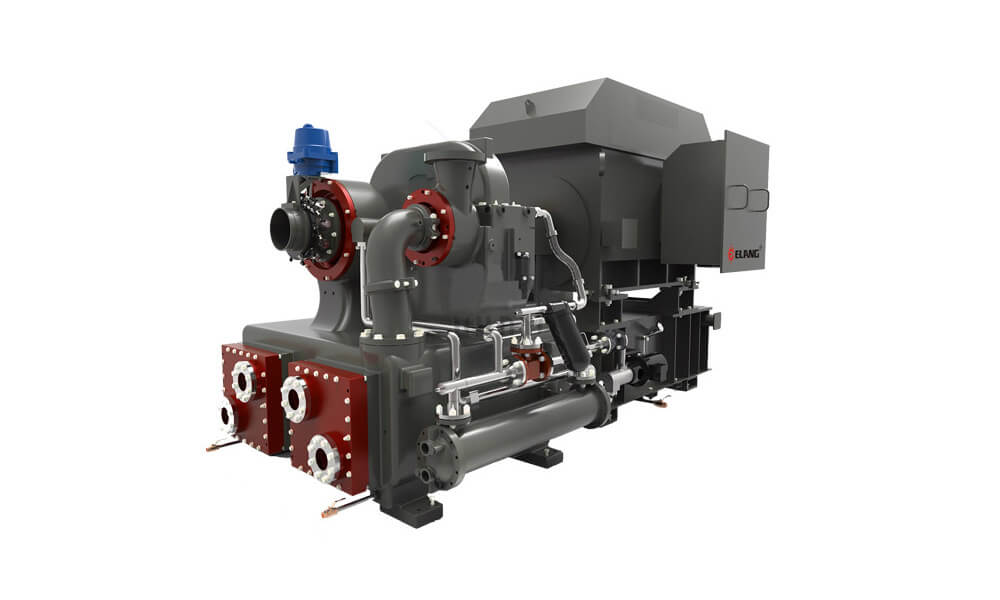
For more details, please contact Elang compressor freely.